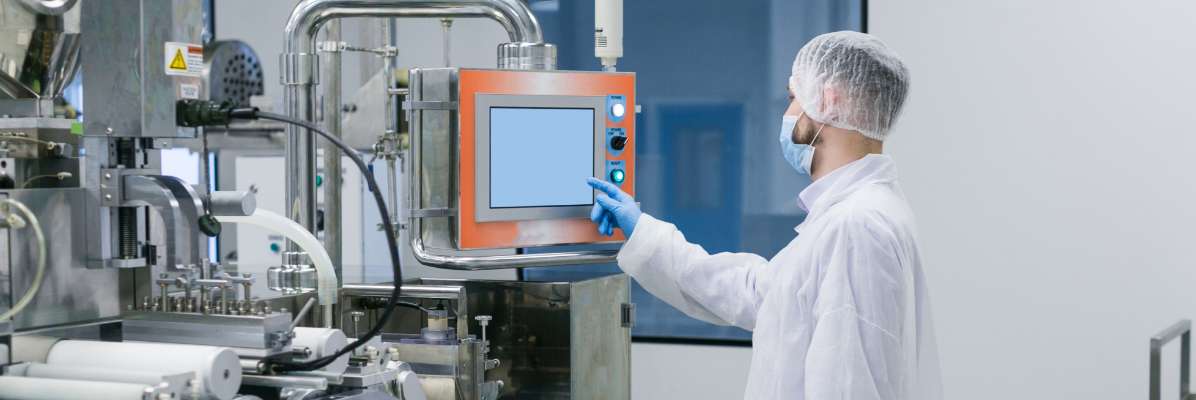
Web converting equipment is automated technology that utilizes control systems for high-capacity production — and it has become an essential part of today’s manufacturing processes. Custom converting equipment reduces labor costs and increases production output to help companies meet the challenges of today’s growing marketplace. This article answers the question, “What is web converting?” and discusses common materials and applications that utilize this diverse manufacturing practice.
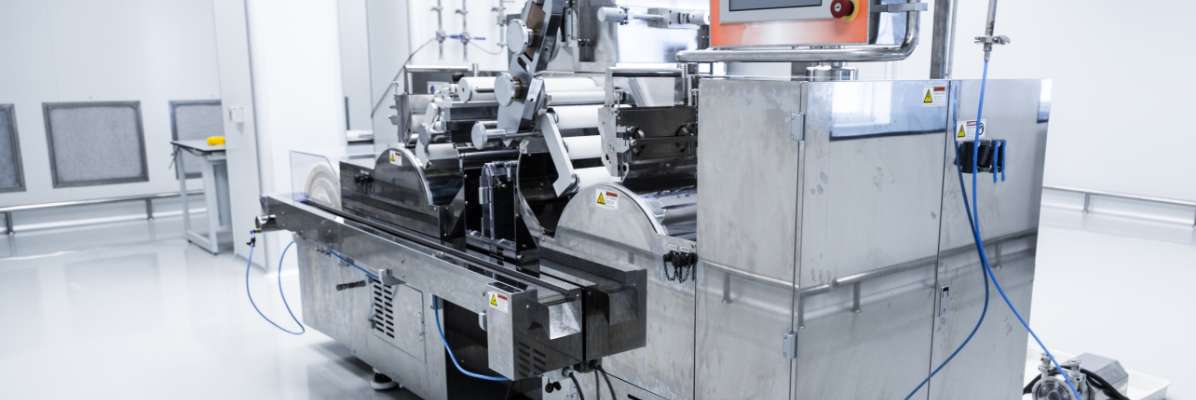
The Basics of Web Converting
Web converting is the process of combining materials into intermediate or finished products. Web converting machinery is highly automated and used in conjunction with conversion technology that allows manufacturers to perform essential functions such as coating, printing, laminating, film sealing and roll-to-roll processing. Proper web alignment and tension control are essential to maintain during manufacturing.
Dozens of industries use web converting equipment to create hundreds of different products. Everything from plastic bags to pharmaceutical equipment and electronics uses web converting machinery during manufacturing. There are hundreds of possibilities for your custom converting line. Here are four typical stages of the web converting process for material goods: Laminating, slitting, die-cutting and finishing.
1. Laminating
At the beginning of the web converting process, two or more materials are combined into a new shape or form. This can include several materials such as adhesives, foam, tape or other substrates.
2. Slitting
A large roll of material such as laminate is cut into a smaller size that matches your application. Slitting as a manufacturing process reduces waste and is more economical for material converting.
3. Die-Cutting
Specific shapes are cut from raw material as the product moves towards finalization. Different web converting equipment is used at this stage depending on the application.
4. Finishing
Specific shapes are cut from raw material as the product moves towards finalization. Different web converting equipment is used at this stage depending on the application.
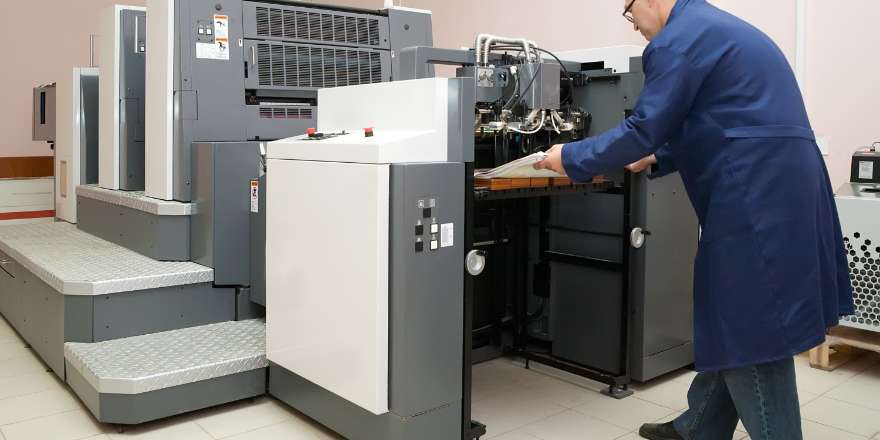
Common Materials Used in Web Converting
Web converting can use several different materials in your manufacturing process. Web converting machinery allows for automating common primary and secondary production activities into a single streamlined event. Each material component used during manufacturing makes up one strand in the web, converting machinery controlled by software and robotics to move it from start to finish. Some of the materials used in web converting include:
- Adhesives
- Laminates
- Film
- Paper
- Plastic
- Metal
Case Study: Web Converting Equipment and Controls
Let’s take a deeper dive into web converting machinery by looking at two of the more common web converting processes: Laminating and coating.
Laminating is a common material converting process where layers are bonded to create a more finished product. In the classroom, a simple form of laminating involves heating plastic and placing a thin layer of it over paper or poster board to give it additional protection and durability. On the other hand, industrial lamination can involve dozens of layers made from several different materials and substrates. Laminating in web converting often occurs at the beginning of the process before materials are cut, printed and finished.
Coating is a similar process where converting equipment applies a protective layer or “skin” onto a product to give the material additional properties that the base product does not have. Coating usually involves a viscous or dry material combined with a liquid to create a protective layer. Powder coating, paints and enamels are good examples of coating products. These are generally applied using a spray nozzle or some other medium at the very end of the manufacturing process. Afterward, the coated product is dried or cured in a prescribed manner.
Both of these processes require rigorous controls to ensure quality and efficiency. Web converting equipment provides that through two main implementations: tension control and web alignment.
Controls are put in place to keep the material at the desired tension as it is fed into the machine for further processing. Without these tension controls, imperfections and inconsistencies would arise during manufacturing. Web alignment is also necessary to keep the materials uniform as they move through the converting equipment. Manufacturers rely on custom converting solutions to handle unique applications or those that require higher levels of regulation and control.
Design Your Web Converting Equipment Solution With South Shore Controls
As automation and controls specialists, South Shore Controls is a single-source provider of custom converting solutions. We have developed web converting equipment and controls for laminating and coating applications. As a customer and design partner, you can leverage our knowledge and expertise into web converting equipment that handles your most difficult projects. Contact South Shore Controls today to learn more about our web converting design and implementation capabilities.