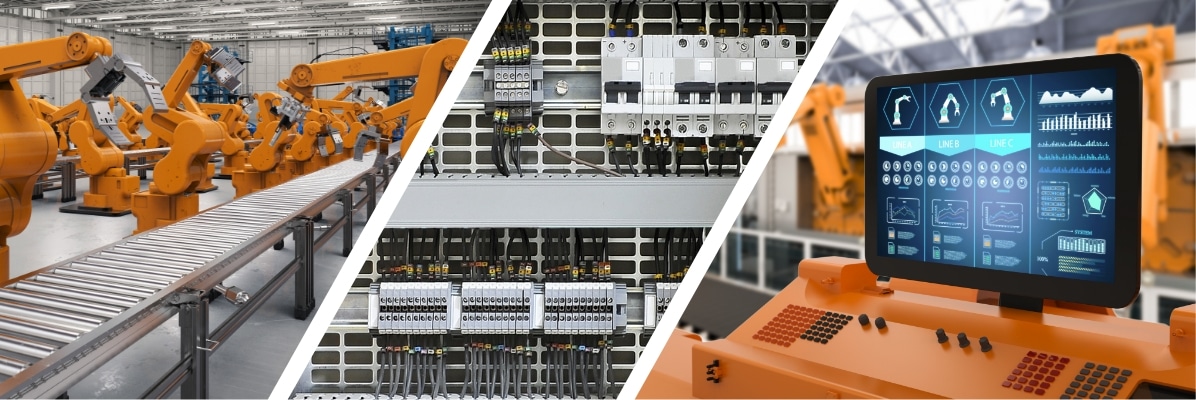
With the rise of modernization and technology, many industries have begun to adopt and embrace industrial automation systems to increase efficiency and productivity at the workplace. The vast adoption of these systems has seen the industrial automation market growing globally, reaching $191 billion in 2021 and expected to grow to a staggering $395 billion by 2029, according to Fortune Business Insights.
While most industrial manufacturers already understand the growing global adoption of industrial automation systems, many don’t have a good grasp of the different types of automation systems and how each can benefit a company. Whether it’s warehouse automation or automated conveyor systems, different types of automation can benefit different types of businesses.
In this article, we will look at what industrial automation is and the different types of industrial automation systems available.
What Is Industrial Automation?
Industrial automation uses control systems, usually computers or robots, to handle manufacturing processes and machines to replace human beings. These systems can operate industrial equipment automatically and typically include feedback loops and sensory programs that can adjust operating conditions automatically to meet the desired values based on real-time data.
Four Types of Industrial Automation Systems
As the statistics above show, there has been huge growth in the use of industrial automation systems. But how do you know what automation system is the right one for your business? The right automation system for you will be determined by:
- Labor conditions
- Competitive pressures
- Work requirements
- Manufacturing and assembly specifications
- Labor costs
There are four types of automation systems: fixed automation, programmable automation, flexible automation and integrated automation. Let’s take a look at each type and their differences and advantages. Then you can try to determine which type of automation system is best for you.
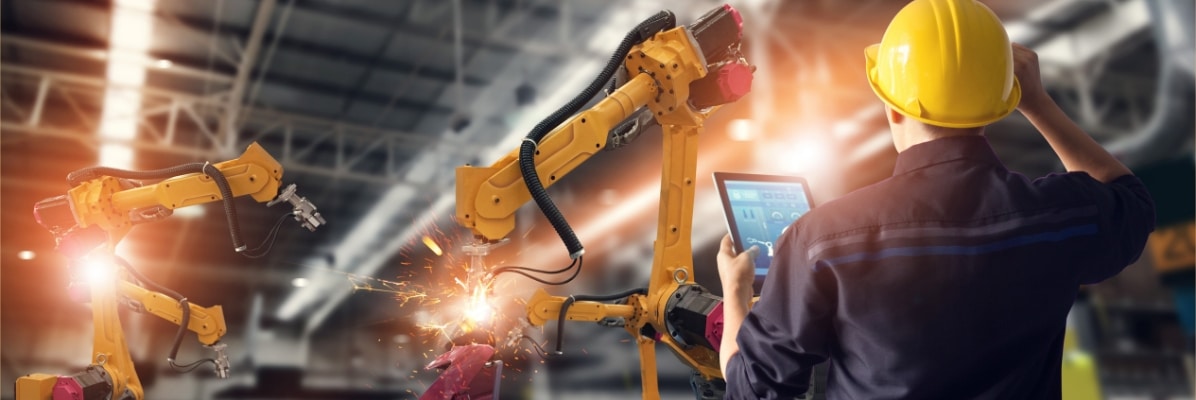
1. Fixed Automation
Fixed automation systems, also known as hard automation, are designed to complete a single set of tasks repeatedly. Fixed automation systems typically are used for discrete mass production or continuous flow systems. An example of a fixed automation system is an automated conveyor belt in the auto manufacturing industry that moves objects with minimal effort, increasing efficiency.
2. Programmable Automation
Programmable automation systems are controlled by commands delivered by a computer program. Because of this, the automated processes can vary based on the instructions sent to the computer by the designer’s code. Programmable automation is commonly used in settings where similar items are produced using the same automated steps and tools. For example, paper and steel rolling mills use the same steps to create many different types of products.
3. Flexible Automationn
Flexible automation, also known as soft automation, is typically used in batch processes with a variety of products. Each piece of equipment is given instructions for a computer operated by a human, so changing code can be delivered to the computer, allowing for more flexible production. The primary advantage of flexible automation is that the product changeovers occur quickly and automatically because they are conveyed by the control system, eliminating the extra time required to reconfigure the equipment in between batches. Industries that use flexible automation include textile manufacturing, food processing or paint manufacturing.
4. Integrated Automation
Integrated automation systems involve totally automating manufacturing plants with minimal human involvement. Computers can be used to design parts, test the completed designs and then fabricate the new parts. Integrated automation can be used with continuous process manufacturing and batch process manufacturing.
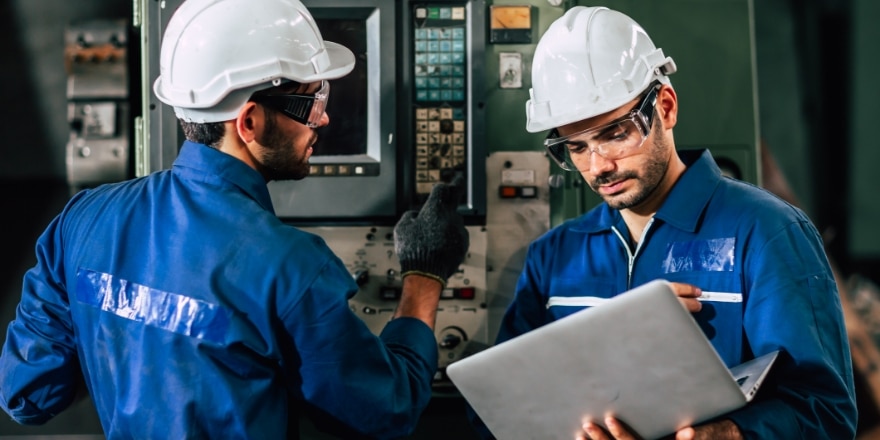
Benefits of Industrial Automation
There are many benefits of industrial automation, including:
- Lower operating costs. Industrial automation systems eliminate the need to pay employee wages and benefits.
- Higher productivity. Companies can hire hundreds of employees to work round-the-clock shifts, but they still need breaks, days off and holidays. Completely automated plants can operate 24/7.
- High-quality products. Automation can help reduce the amount of error associated with human workers creating products, resulting in a higher quality product being produced.
- Greater flexibility. Rather than having to train an employee for a new task, a simple computer code can quickly change a production process.
- Increased safety. Using robots or other types of automation systems can keep workers out of dangerous situations.
- More accurate data collection. Automated data collection gives you access to key production information and reduces your data collection costs, so you can make more efficient decisions about your manufacturing process.
Discover How South Shore Controls Can Help Your Business With Industrial Automation Systems
South Shore Controls offers different types of industrial automation systems and control system upgrades that will help you address your company’s challenges. Our automation system integration allows you to add further capabilities to your current automation system to help you improve efficiency and elevate your quality. Contact South Shore Controls today to learn more about our industrial automation solutions.