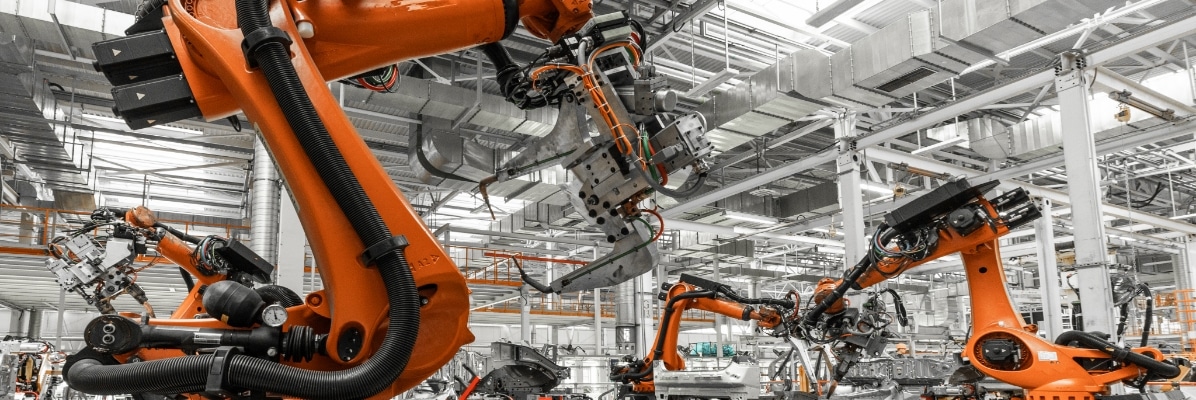
Modern industrial automation technologies have drastically transformed the way various industries operate. No matter the size of your enterprise, industrial automation is increasingly becoming more of a necessity than a choice. According to Fortune Business Insights, the global industrial automation market is expected to grow from $205.86 billion in 2022 to $395.09 billion in 2029.
In this article, we will help you understand industrial automation basics and how South Shore Controls can help your business implement industrial automation systems that can transform your business.
What Is Industrial Automation?
Industrial automation is when control technology is used in manufacturing to eliminate or reduce manual labor. How does it do that? Industrial automation and controls help to streamline systems by integrating smart tools and computers into multiple operations. After initial programming, computers can control manufacturing processes with minimal human intervention.
What Are the Levels of Industrial Automation Systems?
Industrial automation systems can be extremely complicated, so it may be useful to consider the hierarchy of such systems, which consists of four levels with individual systems, software and devices utilized at each level.
1. Field Level
This is the first, most basic level where data is transferred to the control level for further manufacturing processes. This is done through the use of sensors and actuators.
2. Control Level
At the control level, automation devices receive the parameters from the sensors and direct them to the actuators for specific operations.
3. Supervisory and Monitoring Level
Industrial automation tools control the automation process at this level. Everything from the time at which machines start and stop to product goals are established here.
4. Managerial or Information Level
At this highest level, the entire automation system is managed. The managerial, or information, level typically focuses on issues like order tracking, market analysis and sales numbers. The data garnered at this level allows businesses to make the best decisions for managing their automated systems.
What Are the Different Types of Industrial Automation Tools?
Industrial automation systems require specific control systems to integrate devices or equipment with the complete larger system. Some of these industrial automation tools include:
- Artificial Neural Network (ANN): ANN is a computer system used to analyze processes and weigh complicated factors to make a decision.
- Supervisory Control and Data Acquisition (SCADA): SCADA is a system used to acquire and analyze data to enhance decision-making.
- Human Machine Interface (HMI): HMI allows communication between the human operators and the automated systems.
- Distributed Control System (DCS): A DCS is a monitoring control designed to facilitate communication between the various tools used in the industrial automation process.
- Process Control System (PCS): The code of a PCS will monitor results and adjusts processes as needed. An example of closed-loop” automation.
- Programmable Logic Controller (PLC): A PLC is a control system that automates electromechanical processes and can make changes based on exterior inputs.
What Are the Benefits of Industrial Automation?
Factory automation systems offer many advantages for manufacturers. Four of the biggest benefits of industrial automation systems are:
Productivity
Industrial automation applications increase the speed and accuracy of actions, which means that more products can be made in less time, reducing costs.
Safety
Having fewer workers involved in manufacturing processes improves safety rates, as dangerous operations can be automated. Also, automated systems can identify potential dangers before they occur.
Efficiency
Industrial automation systems use well-defined processes that can be controlled within guidelines specified by human programmers, reducing the chance for human error.
Quality
With automation, quality control has been simplified. More variables can be controlled by automation systems, reducing the possibility for error. Industrial automation systems are capable of detecting errors quickly through self-diagnostic checks.
Improve Efficiency and Safety With South Shore Controls’ Industrial Automation Solutions
South Shore Controls is a full-service industrial automation systems service provider. Our experienced staff creates usable industrial automation solutions to meet your company’s challenges. Whether you are looking for a control system upgrade or new control system integration, we can guide you through every step of the process and help your company improve efficiency, safety and productivity. The process will begin with a plant tour and meeting that analyzes your needs and outlines your wishes. Then we will listen to your feedback, giving you the control you want as we work together to improve your processes.
Discover the Difference South Shore Controls Can Make
Since 1995, South Shore Controls has been helping customers in Ohio, Michigan, Indiana and Pennsylvania overcome challenges every day. Our collaborative project development team will work closely with you and your team to find the ideal industrial automation solutions to your problems. Contact us today for the assistance you need.