Metal Forming Service
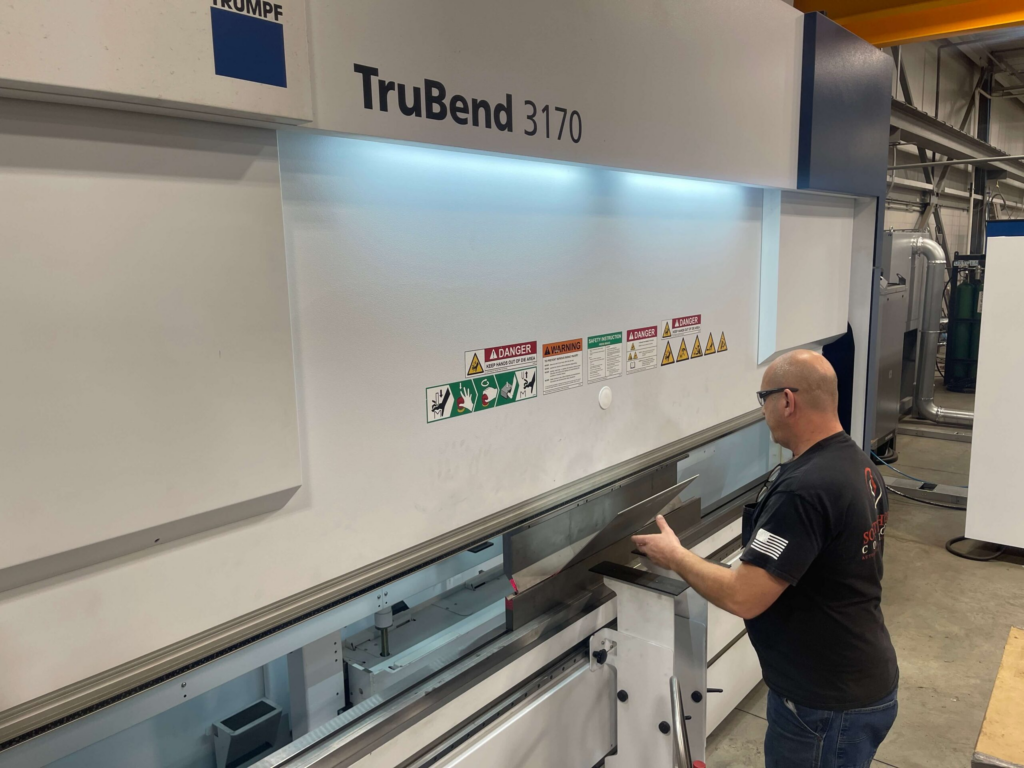
TRUMPF TruBend 3170 3 AXIS BACK GAUGE
MAX
- Tonnage: 187
- Bed Length: 10′
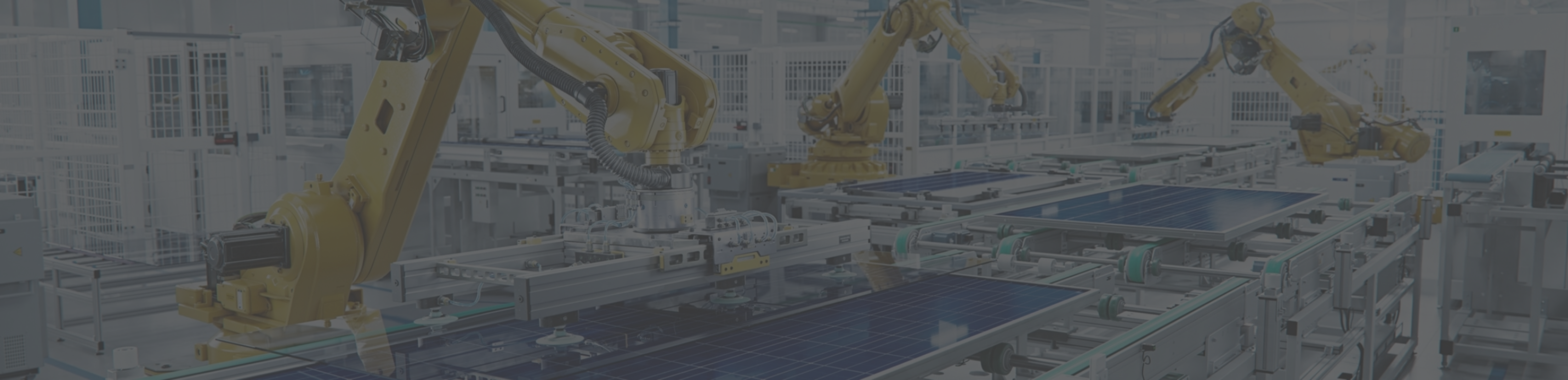
The Value of Outsourcing Forming Operations
- Cost Efficiency: Outsourcing metal forming operations can lead to cost savings for manufacturers. Contracting with specialized metal forming providers often allows access to advanced technologies and expertise without the need for significant upfront investments in machinery, equipment, and skilled labor.
- Expertise and Specialization: Metal forming service providers typically specialize in specific processes such as stamping, bending, or extrusion. By outsourcing to experts in the field, manufacturers can benefit from the specialized knowledge and skills of professionals who focus exclusively on metal forming, leading to higher-quality products and improved efficiency.
- Focus on Core Competencies: Outsourcing allows manufacturers to concentrate on their core competencies, such as product design, marketing, and overall business strategy. Metal forming can be a complex and specialized process, and by outsourcing this aspect of production, companies can streamline their operations and enhance overall efficiency.
- Flexibility and Scalability: Outsourcing provides manufacturers with greater flexibility and scalability. Metal forming needs may vary based on market demand, and outsourcing allows manufacturers to quickly scale production up or down without the challenges associated with maintaining an in-house metal forming facility.
- Access to Advanced Technologies: Metal forming service providers often invest in state-of-the-art technologies and equipment to stay competitive. By outsourcing, manufacturers can leverage the latest advancements in metal forming without the need for continuous capital investments in upgrading machinery.
- Reduced Lead Times: Specialized metal forming providers often have streamlined processes and workflows, leading to shorter lead times for product completion. This can be crucial for manufacturers facing tight production schedules or responding to changes in market demand.
- Risk Mitigation: Outsourcing metal forming operations can help mitigate certain risks associated with in-house production, such as equipment maintenance, skilled labor shortages, or market fluctuations. Service providers are often equipped to handle these challenges, allowing manufacturers to focus on core business activities.
- Global Sourcing Opportunities: Outsourcing provides the opportunity to explore global markets for metal forming services. Manufacturers can tap into a broader pool of suppliers, potentially benefiting from lower labor costs, diverse skill sets, and access to a variety of materials.
- Quality Assurance: Reputable metal forming service providers often have stringent quality control measures in place. Outsourcing to such providers can ensure that the manufactured components meet or exceed industry standards, contributing to the overall quality of the final product.
Project Gallery
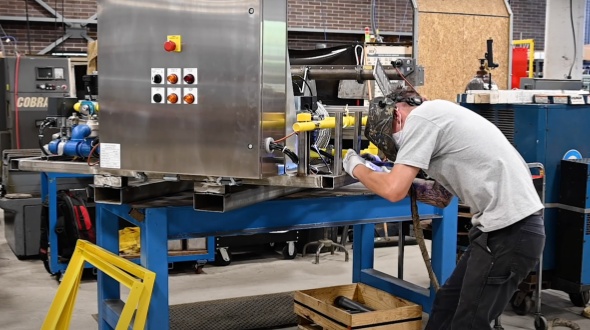
Automation System Integrations You Can Trust
Our years of experience mean you get the automation systems integration that meets your needs, complete with custom-developed code and software. South Shore Controls employs an integrated approach that simplifies the process for you yet delivers the high quality and return on investment that you require.
Our automation system integrations help you lower costs, boost productivity, enhance workflow efficiencies and improve product quality. We can help you gain greater flexibility to meet the needs of modern manufacturing. From design to installation and training, we handle every facet of your project. Contact us to learn more.
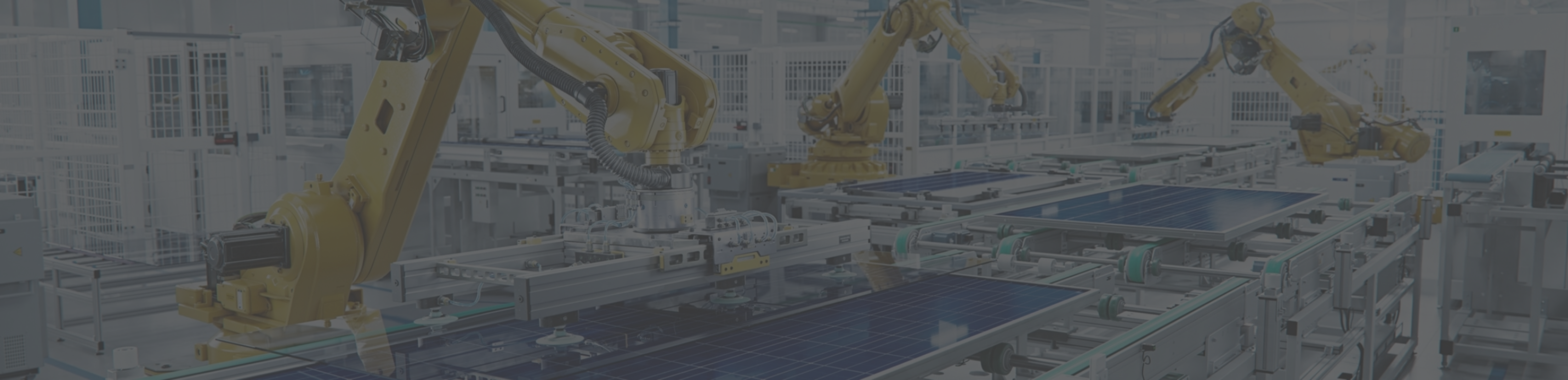
Automation System Integration Capabilities Include These Areas of Expertise:
- Control Panels
- Batch Process Controls
- PLC Programming
- HMI Programming
- Drive Systems
- Control System Retrofits
- Specialized Machinery
- Pick & Place Robotic Systems
- Conveying/Material Handling
- AC and DC Drives & Motion Control Upgrades
- Position & Presence Monitoring
- Temperature Sensing and Control Systems
- Available in 3 models: SM, MD, LG
- Axis options: X, X & Z, X & Z with control
Frequently Asked Questions
What is system integration?
System integration is the process of introducing automated systems to help improve the functionality of your overall operation. Examples of automation system integrations include adding robotic pick and place systems or implementing position and presence monitoring.
What is the system integrator’s role in automation?
At South Shore Controls, the industrial automation systems integrator’s role is to provide a one-stop-shopping approach to your project, delivering the design, manufacturing and installation of your automation system integration.
What are system integration challenges?
Challenges to a successful automation system integration include:
- Sourcing the right components
- Developing the correct technology interfaces
- Creating control and field instrumentation documentation
- Planning for future expansion
What is a legacy system integration?
In a legacy system integration, South Shore Controls incorporates new, modern systems to upgrade or replace equipment that is obsolete or near the end of its lifecycle.
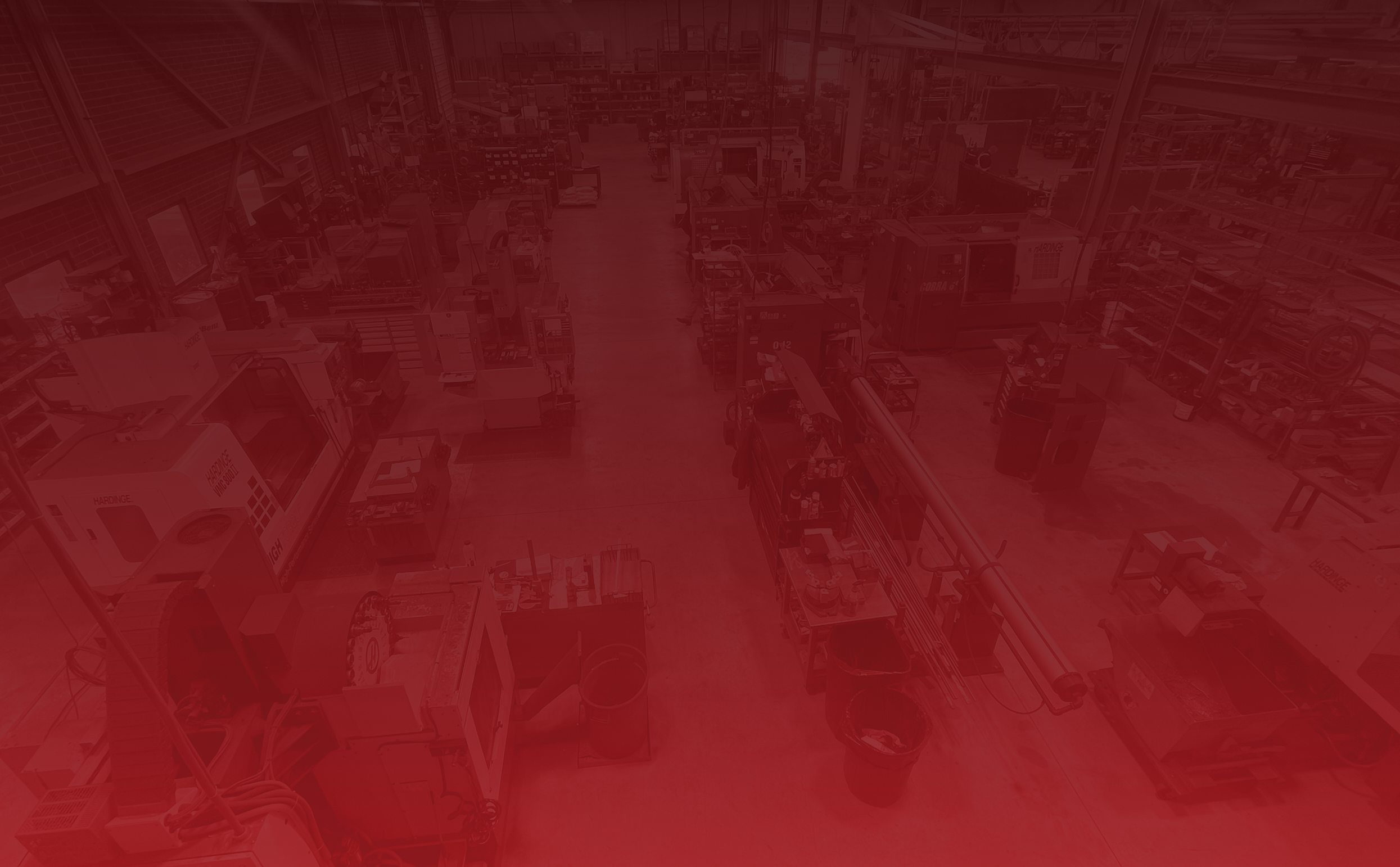
Discuss Your Project with Our Team Today
Contact our automation and controls experts to learn how we can help improve and automate your manufacturing processes.
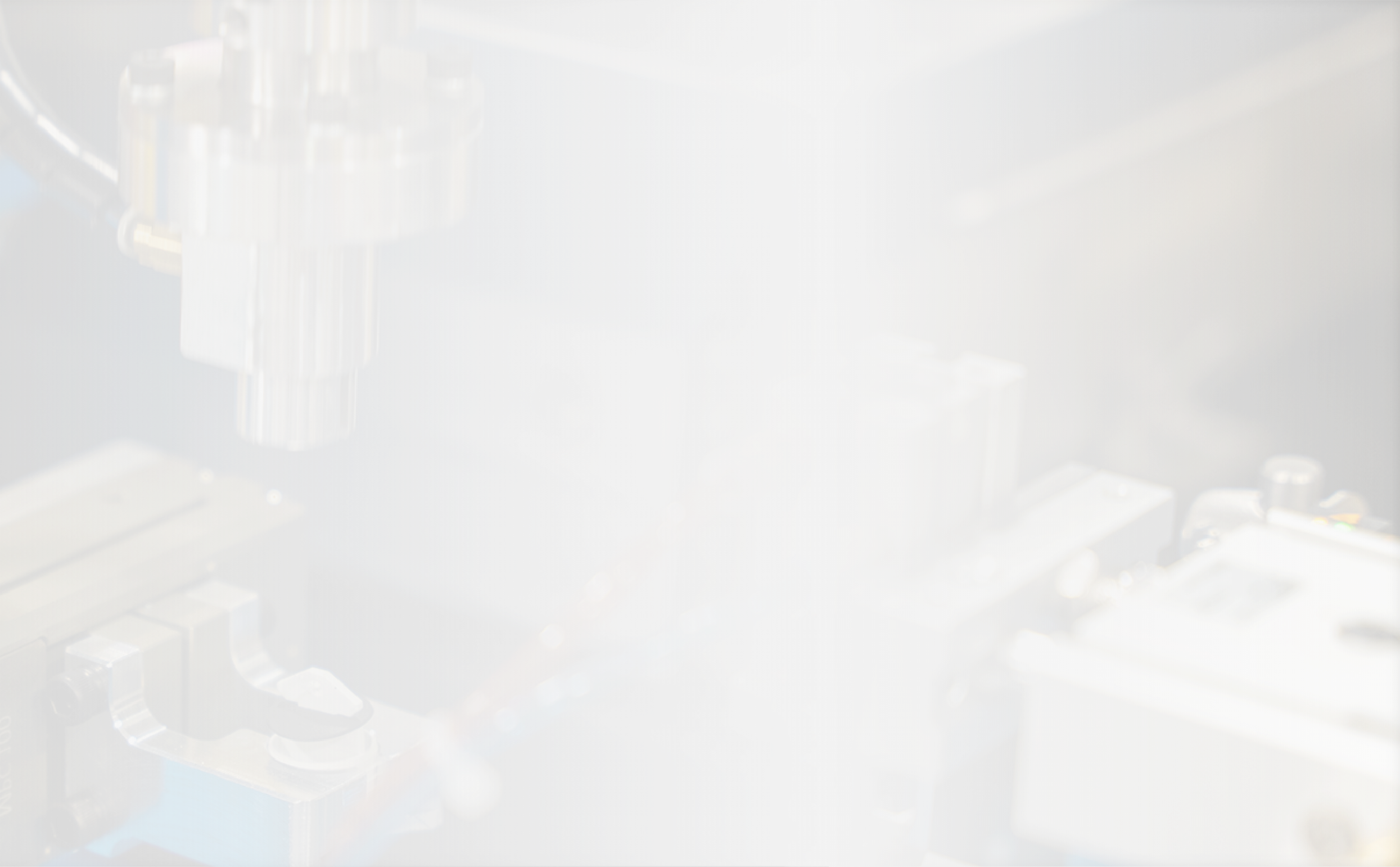